Please Click Here To View The Video
Seamlock 760 Roof Panel Roll Forming Machine
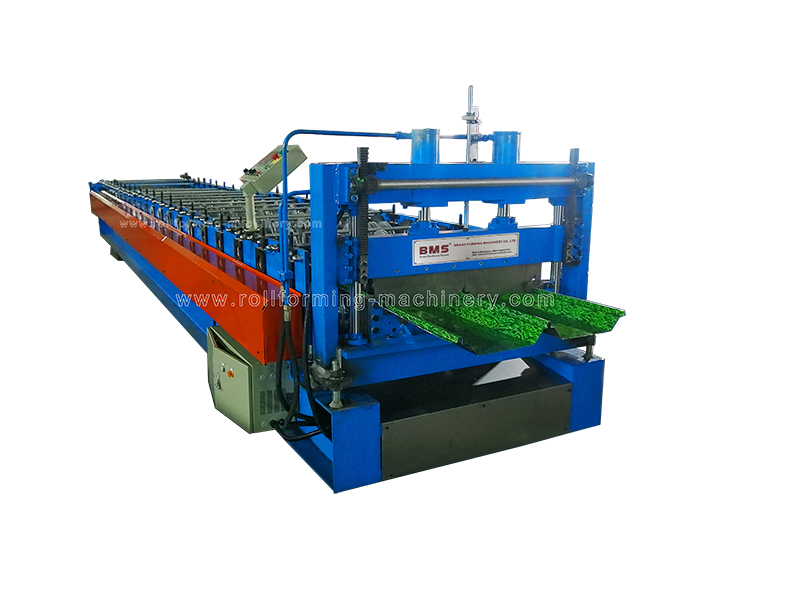
Profile
Seamlock760 Rood Panel Roll Forming Machine, that is, Y=51 means height, X=760 means width
Fastener Building Method 1 Fastener Building Method 2 Fastener Building Method 3
Material
Effective Width: 1219mm Wave Distance Tolerance: ±1mm
Material Thickness:0.6-0.8mm Wave Height Tolerance: ±1mm
Inspection Thickness:0.6mm Valid Width Tolerance: ±2mm
Applicable Material: Color Coating With Yield Strength: 300Mpa
Test Material: two weeks before the machine trial run, BMS Group provides the feeding size to the buyer for purchasing.
Work Flow
Uncoiler -- Manual Pre-Cutting -- Feed Guide Device -- Roll Forming Mill -- Hydraulic Post- Cutting Device -- PLC Control System -Hydraulic System -- Exit Rack
Machine Components
1) Manual Uncoiler
Manual control steel coil inner bore shrinkage and stop
Max Feeding Width:1250mm
Coil ID Range:508±30mm
Max capacity:5ton
2) Manual Pre-Cutting
With Manual pre-cutter for easy operation and save material: The pre-cutter is conneted with PLC control system, PLC is calculating profile length within roll forming. Once material is required to change, PLC is calculating the length for total quantity and remind operator,production finishes and able to manual shearing material before roll forming so as to change material for new production. It is the advanced function and good for production to save material, avoid wasting. The rest sheet is continuous formed by forming system.
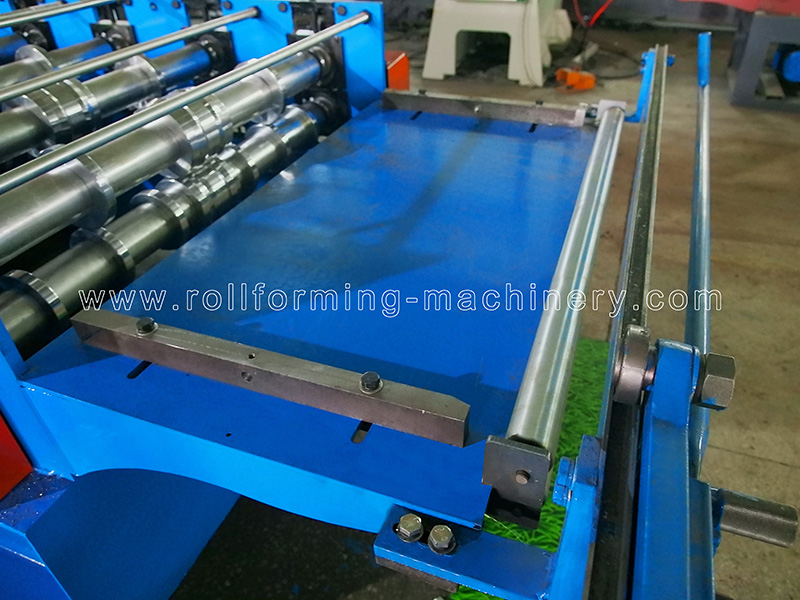
3) Roll Forming Machine
Body Base H450 by welding;
The side plate thickness to adopt the Q235t18mm;
The roller is made of 45# steel with hard chromium 0.04mm after finishing, Wire drawing polishing roller
shaft diameter Ø75mm (45# steel);
Gear chain drive,18 Station roll forming;
Main motor 7.5 KW, reducer R series;
Forming speed: 12-15 m/min.
4) Hydraulic Post Cutter
Post to cut, stop to cutting,Three pieces type of cutting blade design, no blanking;
Hydraulic motor: 3.0KW; Cutting pressure: 0-16Mpa;
Cutting tool material: Cr12Mov (= SKD11 with at least one million times of cutting life), Heat treatment to HRC58-62 degree;
The cutting power is provided by the independent engine hydraulic station (Look Below).
5) PLC Control System
Control The Quantity And Cutting Length Automatically;
Input The Production Data (Production Batch, pcs,Length,etc.) On The Touch Screen;
It Can Finish The Production Automatically;
Combined With: PLC, Inverter, Touch Screen, Encoder, etc.
6) Exit Rack
After-Sale Service
1. The warranty is 24 months after the client receives the machine and
within the 24 months, we will courier the replacement parts to the client free of charge;
2. We offer technical support for the entire life of our machines;
3. We can send our technicians to install and train the workers in the clients' factories with
extra cost.
Packing method
Main body of machine is naked and covered by plastic film (to protect of dust and corrosion), loaded into container and steadily fixed in container suitable by steel rope and lock, suitable for long-distance transportation.
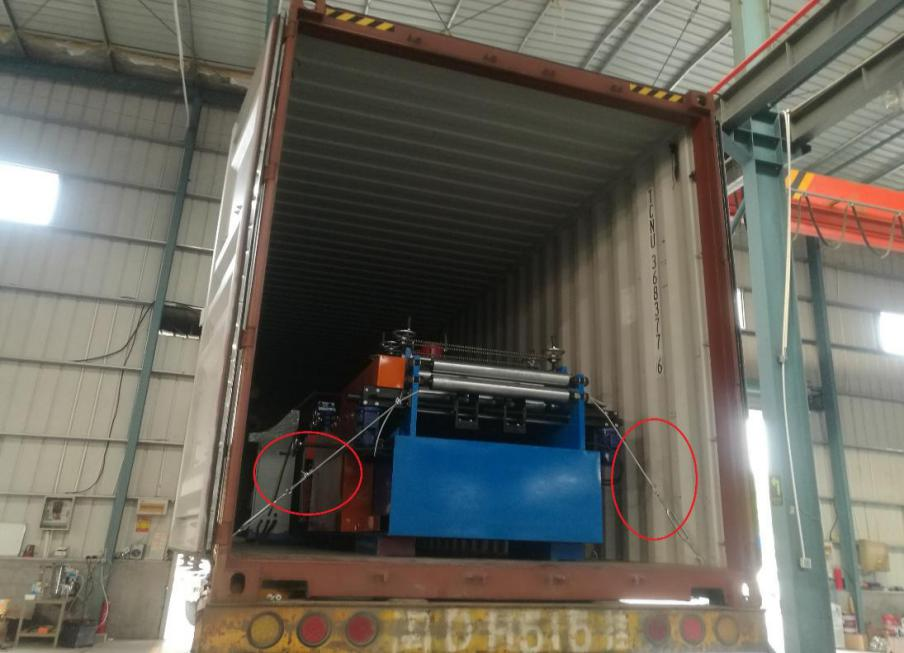